Overview
Control valves are essential components in various industrial processes, enabling precise regulation of fluid flow, pressure, and temperature within a system. Control valves guarantee the best possible performance, safety, and efficiency in industrial operations by modifying the flow of liquids, gases, or slurries. Oil and gas, chemical manufacturing, electricity generation, water treatment, and pharmaceuticals are just a few of the industries that depend heavily on these devices.
What are control valves?
Control valves are mechanical devices that change the size of a flow passage to control the flow of fluid to desired devices, like reactors, turbines, or heat exchangers. They are essential for keeping process parameters including pressure, temperature, and flow rate within predetermined bounds and can be operated manually or mechanically.
Depending on the application and sector, the fluids that pass-through control valves can differ significantly. Typical fluids consist of:
Water, crude oil, refined petroleum products, and chemicals are examples of liquids.
Gases include nitrogen, oxygen, steam, and natural gas.
Slurries are mixtures of solid and liquid particles, like those produced during chemical processing or mining..
Usually, these valves are made up of three major components:
The Valve Body: The primary flow regulation component.
The Actuator: Responsible for moving the valve to its open or closed position.
The Positioner: Ensures the valve achieves the desired position as per control signals.
Control valves are widely used in industries such as:
Oil and Gas: Regulating crude oil and gas flows in pipelines.
Chemical Processing: Managing reactive chemicals with precision.
Power Plants: Controlling steam and water flow for turbines.
Water Treatment: Regulating water flow in purification processes.
Pharmaceuticals: Ensuring accurate dosing in drug production.
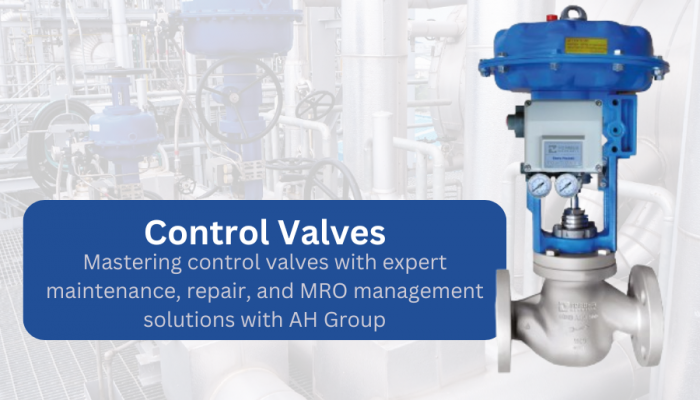
What causes control valves to fail?
Even with their sturdy construction, control valves can malfunction for a number of causes which could cause major downtime and operational disruptions. Typical reasons for failure include:
Wear and Tear: Seals, seats, and diaphragms are among the valve components that might deteriorate with continuous use.
Corrosion: Parts of valves may corrode when exposed to severe chemicals or environments.
Blockages: Debris or foreign objects accumulating can prevent fluid flow.
Actuator Malfunction: Inadequate actuators may make it difficult for the valve to open or close as intended.
Inappropriate Sizing or Selection: Using a valve that isn’t appropriate for a certain procedure can cause it to fail too soon.
Improper Maintenance: Ignoring minor problems might cause significant breakdowns if regular inspections and servicing are not performed.
How can you prevent control valves from failing?
A proactive strategy that incorporates appropriate selection, installation, and maintenance procedures is necessary to prevent control valve failure:
Pick the Correct Valve: Pick a valve that is appropriate for the particular process parameters, including fluid type, temperature, and pressure.
Frequent Maintenance: To identify wear, corrosion, or obstructions early on, do routine inspections.
Correct Installation: To prevent misalignment or excessive strain on valve components, make sure that the right installation techniques are used.
Track Performance: To keep tabs on valve performance and identify possible problems before they become more serious, use diagnostic tools.
Prevent Corrosion: In areas with severe chemicals, apply coatings or materials that are resistant to corrosion.
Training: To guarantee correct handling and troubleshooting, give operators and maintenance staff sufficient training.
How can control valves be repaired?
In order to save downtime, prompt and efficient repairs are essential when control valves fail. Usually, the repair procedure entails:
Diagnosis: Use diagnostic instruments or visual examinations to determine the failure’s primary cause.
Component Replacement: Change out worn-out or broken components, such as actuators, seats, or seals.
Cleaning: Clear away any obstructions or debris preventing fluid movement.
Recalibration: To guarantee correct operation, adjust the positioner and actuator of the valve.
Testing: To ensure that the repaired valve satisfies performance requirements, conduct operational tests.
Documentation: To track the valve’s history and guide future maintenance, keep thorough records of all repairs.
Additionally, it is imperative to seek a professional repair partner for repairing control valves. Inadequate repairs made by untrained professionals raise the possibility of recurring malfunctions and additional disruptions to operations. Expert repair services guarantee accuracy, adherence to industry norms, and increased valve longevity.
Control valves are essential to industrial operations because they provide both operational safety and efficiency. To increase their longevity and dependability, it is crucial to comprehend their purpose, possible failure modes, and maintenance needs. Businesses may minimize downtime, maximize performance, and protect their operations by implementing preventive measures and quickly resolving problems. Control valve maintenance and repairs are investments that pay off in the long run by increasing efficiency and lowering costs.
Interested in learning if an industrial repair management partner is the right fit for your industrial facility or manufacturing plant? Contact us at info@ahgroupna.com