In today’s industrial landscape, plant managers face the formidable challenge of maintaining operational efficiency while adhering to tight budget constraints. Every decision must balance cost-effectiveness with the need for reliability and performance. Amidst this balancing act, the maintenance of machinery, including maintaining critical spare parts, stands out as a crucial opportunity for cost savings. Through strategic industrial repair management and the refurbishment of machine components, plant professionals can significantly reduce maintenance costs. Effective critical spare parts management ensures that essential components are readily available, freeing up the budget to be allocated to different departments.
Saving on Maintenance Through Repair
One of the most direct ways to cut maintenance costs is by opting for the repair of malfunctioning or worn-out machine components instead of replacing them with new components. Repairing components often costs significantly less compared to purchasing new ones, especially for high-value equipment where parts can be expensive. By focusing on repairing specific failed components, plant professionals can extend the lifespan of existing machinery and avoid the substantial cost required for new equipment.
For instance, a broken servo motor or a damaged gearbox can often be repaired with precision machining or welding techniques, restoring them to optimal functionality. The cost of such repairs is typically a fraction of the price of a new component, and the turnaround time is generally shorter, minimizing downtime.
Effective critical spare parts management is crucial here. By maintaining an inventory of critical spare parts, plant professionals can ensure that essential components are readily available for repair. This proactive approach reduces downtime and ensures that machinery remains operational without unnecessary delays.
Working with an MRO repair management partner can help in-plant teams cut costs by leveraging economies of scale, as well. MRO repair management partners have high volumes of components needing repairs, which allows them to negotiate preferred pricing with repair suppliers, saving plant professionals even more on industrial repair costs.
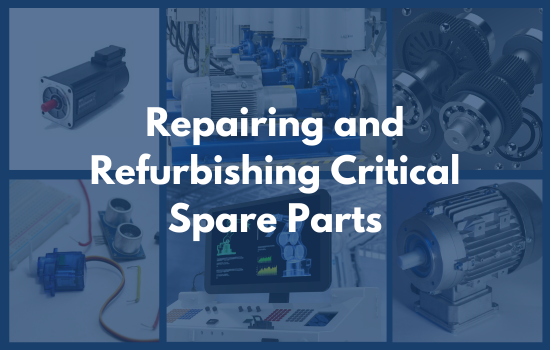
Saving on Maintenance Through Purchasing Refurbished Machine Components
Another effective strategy to save on maintenance costs is through purchasing refurbished machine components. Refurbished parts are pre-owned components that have been restored to their original condition or better, often undergoing rigorous testing and quality control processes. These components offer a cost-effective alternative to brand-new parts while providing comparable performance and reliability.
Purchasing refurbished components can lead to significant cost savings, especially for expensive or hard-to-find parts. For example, a refurbished set of industrial rubber rollers, a gearbox, or a servo motor can be acquired at a fraction of the cost of a new one, without compromising on quality or longevity. Many suppliers of refurbished components offer warranties and support, further ensuring the reliability of these parts.
Effective critical spare parts management is crucial in this approach. By maintaining an inventory of critical spare parts, plant professionals can ensure that essential components are readily available, further reducing lead times. Refurbished parts are often readily available from industrial repair management partners, eliminating the lengthy wait times associated with manufacturing and shipping new components. This quick availability helps minimize downtime and keeps production lines running smoothly.
Opting for refurbished components also supports sustainability by reusing materials and reducing the demand for new manufacturing. This eco-friendly approach aligns with the growing emphasis on corporate social responsibility and can enhance a company’s reputation among environmentally conscious stakeholders.
In the relentless pursuit of operational efficiency, plant managers must navigate the constraints of tight budgets. Repair and refurbishment of machine components offer practical and effective strategies to drastically cut maintenance costs. By embracing these approaches, plant professionals can not only extend the life of their equipment but also free up valuable financial resources. These savings can then be redirected toward other critical areas such as process improvements, employee training, and technological upgrades, ultimately creating a more robust and competitive operation. Through intelligent maintenance practices, including effective critical spare parts management and collaboration with industrial repair management partners, plant managers can achieve the delicate balance between cost savings and operational excellence.
Ready to start saving on maintenance costs? Contact us at info@ahgroupna.com to learn more about how we can help you save up to 70% on your MRO budget.